MES - MANUFACTURING EXECUSION SYSTEM
MANUFACTURING
EXECUSION
SYSTEM
製造実行システム「MES」とは?
合理的で素早い判断、時間や材料等のロス削減に役立ちます
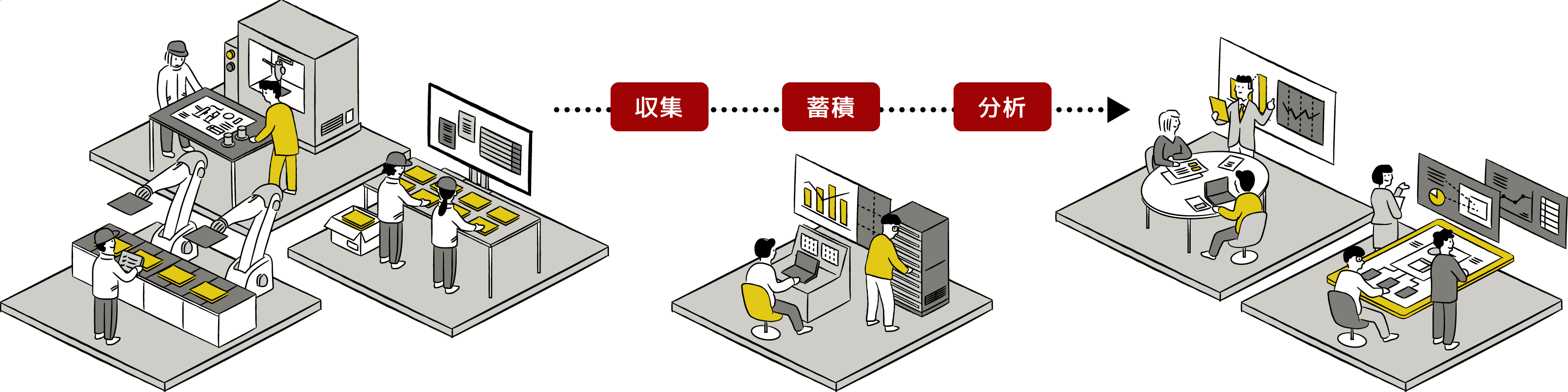
工場内で起こっている問題がリアルタイムで共有できない。トレーサビリティの改善や、過去の事例が活かしきれていない。人や時間、材料などのロスが減らないなど、製造現場における見過ごしがちな改善点は、やがて、小さな積み重ねが大きな差となって現れるもの。
製造実行システム「MES」は、工場内の設備や工程からデータを自動で収集。現場で起きている様々な事象をリアルタイムで共有し、素早く合理的な判断を可能にします。
また、長期間の運用によって蓄積されたデータは、改善点の発見や、経験や勘に頼っていた曖昧な部分を「見える資産」として最適な分析・対策・改善に活用できる強みとなります。
MESは製造効率を見える化し、さらなる伸びしろを発見するツールです。
製造実行システム「MES」は、工場内の設備や工程からデータを自動で収集し、リアルタイムで社内共有するシステムです。システムから得られる正確で鮮度の高い情報は、問題の早期発見や分析をロジカルに行う効果をもたらします。さらに、運用期間が長くなるほどに価値のあるデータが蓄積され、質の高い対策・改善サイクルが見込めるようになるのも特徴です。
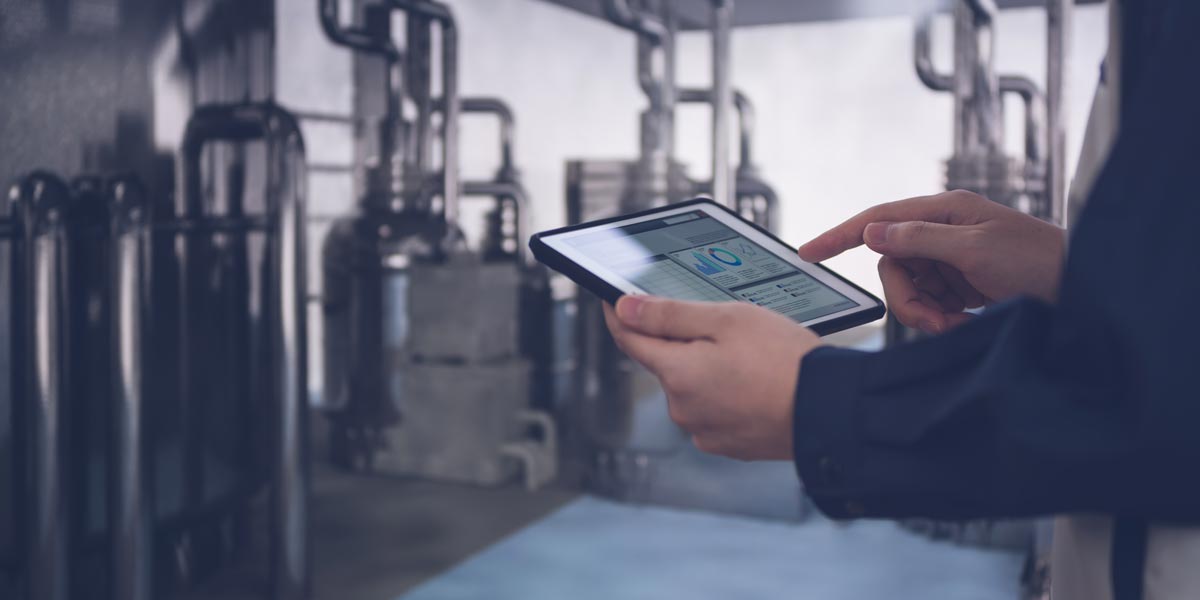
生産ラインの管理
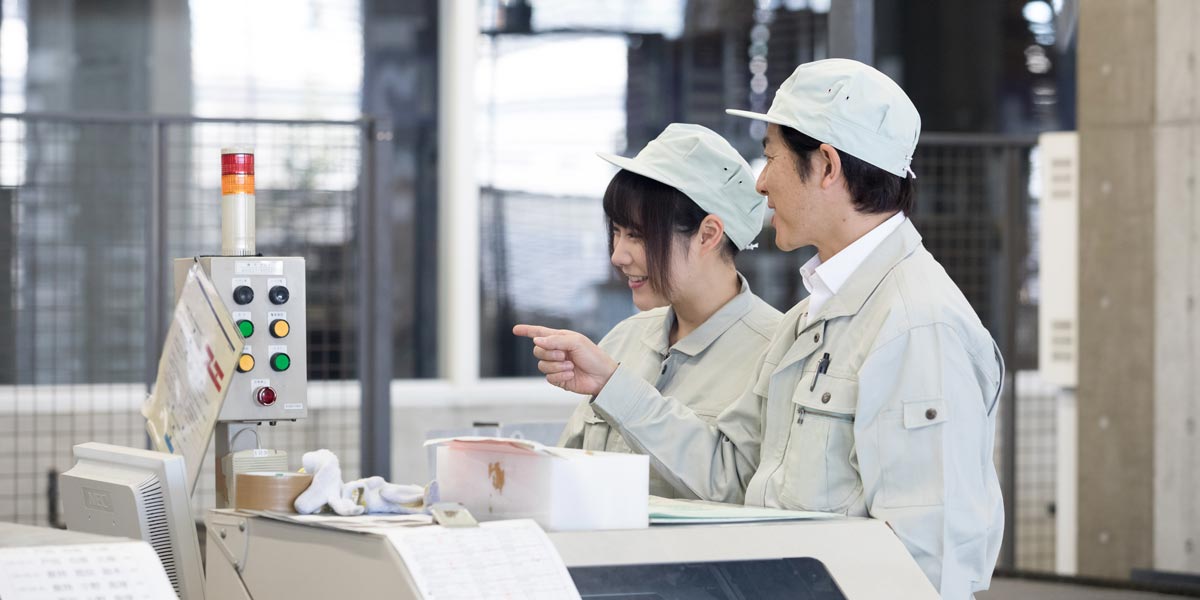
スキルの可視化
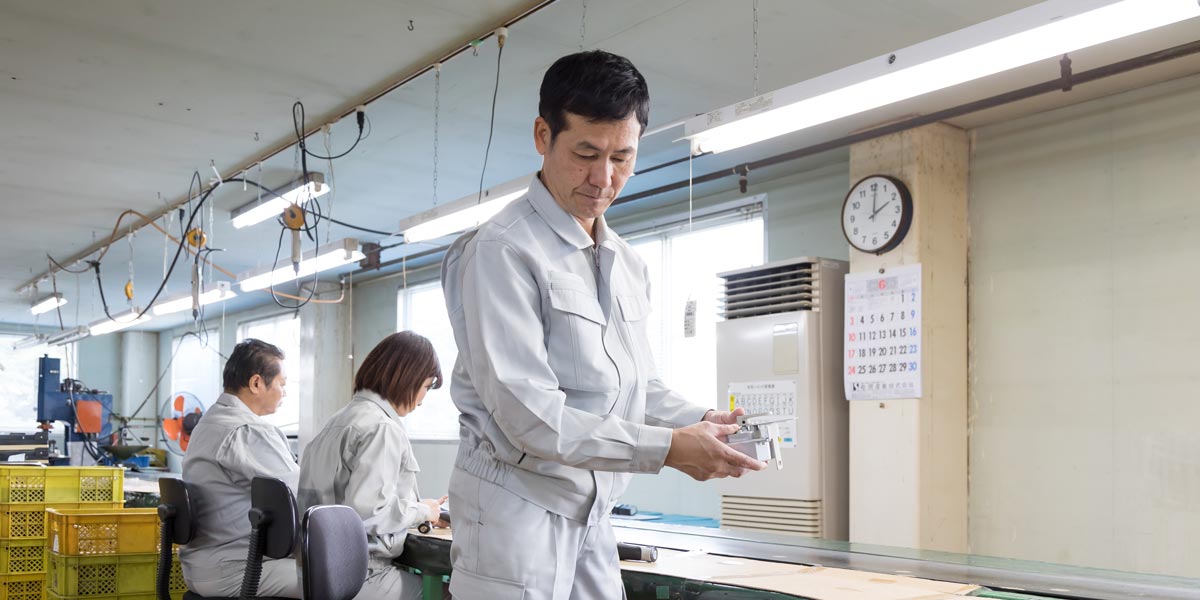
生産時間の可視化
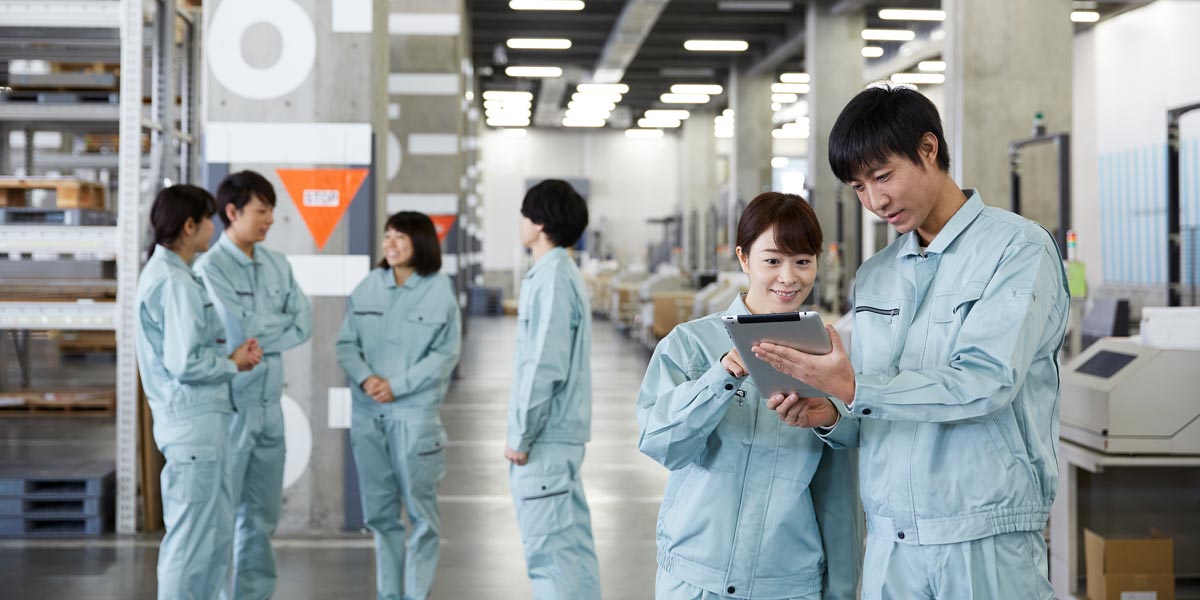
業務の負荷軽減
製造現場の「今」を知り、
課題の改善をスピーディーに
「今」の情報を常に把握することで、機械の稼働・非稼働の状況把握も容易になり、これまでは気が付かなかった無理・無駄を削減。データを元にした判断で、正確な改善ポイントを抽出することができ、短いサイクルでスピーディーな課題の改善につながります。
正確でフラットな共有データで
合理的な意思決定が可能に
作業現場、管理者、経営陣の異なる目線で、同じ共通のデータを確認できるようになる。それぞれの現場担当者の解釈が入った情報ではなく、リアルタイムで抽出されるフラットな情報で共通認識を持つことで、管理者、経営陣は的確な意思決定が可能になります。
ペーパーレスで紙資源の削減
エラー・コスト・遅延の改善
ペーパーレスは紙資源の削減をするだけでなく、情報の集計にかかる時間を飛躍的に早めることができます。また、エラーや遅延の情報をリアルタイムで集計することで、その場で対応・改善できるようになり、コスト管理にも大きく貢献することになります。
紙や手書きの運用でロスやミスが多い
手書きの指示書や日報、検査記録を運用していると、人為的ミスによる不正確さや、文書作成にかかる時間のロス、紙資源のロスは避けられません。
ホワイトボード等による時差ありの情報共有
午前の情報を午後の始業時に共有する、ロットを終えた段階で情報を書き込むなど、手書きによる情報共有では必ずタイムラグが生じます。
紙から基幹システムへの実績入力が手間
製造業務の傍らで、ERP 等の基幹システムへの入力を強いられることは製造以外の工数を増やすことになり、従業員の負担にもなっています。
「まだ大丈夫」が起こす設備停止と不良発生
設備や機械のメンテナンス時期、精度のバラつきを経験則に頼っていると、ミスや予測が外れることもあり、稼働時間や原材料のロスが生じます。
クレーム対応、原因究明に時間がかかる
クレームによって製品の不良が発覚。部品や材料を遡って原因の究明と対策を講じるにも、大量の書類から調べるには人手と時間が掛かります。
予期せぬドカ停によるロス
長時間にわたり自動設備が停止・空転してしまう「ドカ停」は、発見が遅れると大きな時間のロスを生んでしまいます。
文書の電子化で作業軽減&精度向上
手書きや経験則による入力がなくなることで、データ精度の向上と、入力作業軽減による製造コストの削減が見込める。紙資源のロスも削減。
離れた場所でも瞬時に情報共有ができる
工場と事務所、本社と各拠点間の情報がリアルタイムで共有されることにより、工場や工程間の連携、経営判断を迅速化します。
基幹システムと自動連携で間接工数を軽減
生産管理システムなどの基幹システムと自動連携することにより、実績入力などの間接工数を削減。正確な生産実績で生産計画の精度が向上します。
事前検知による予防や対応準備が可能
設備からのデータを監視し、消耗品の交換時期や余地保全を行うことで、適切な準備が可能。保全人員の工数削減や不良によるロスを削減。
トレーサビリティを高めて素早く問題に対応
クレームが出た製品の素性を素早く調べることができ、原因の部品や材料までを遡って横断的な対応や再発予防を迅速に行うことができる。
自動機械の停止をリアルタイムに通知
自動設備の稼働データをリアルタイムに監視し、停止やトラブルが起きた際にアラート通知されるため「ドカ停」の発生を防ぐことができます。
データ収集が生む改善のサイクル
MESは工場内にある様々な工作機械や検査機器、作業員からの入力によるリアルタイムなデータを収集し、社内に共有します。そこから得られる正確で鮮度の高い情報は、問題の早期発見や分析をロジカルに行う効果をもたらします。さらに、運用期間が長くなるほどに価値のあるデータが蓄積されるので、質の高い対策・改善サイクルが見込めるようになります。
ERP(基幹システム)との連携
MES の役割は、工場の設備や原材料、仕掛品などの数量や状態などをリアルタイムに把握し、生産計画に基づいて作業のスケジュールを組み立てたり、作業者への指示を出したり、作業手順に関する情報を収集管理することにあります。さらに、企業内の基幹システム(ERP など)とのシームレスな連係を構築することで、生産計画の精度向上に役立ちます。
一般的なデータ収集設備の構成例
MESが製造現場の設備や工程からデータを収集する際は、下記のような構成が一般的です。自動設備(機械)では、機種側のデータ通信機能や各社のPLC やOPC-UA からデータ取得を行い、通信機能のない設備では制御盤へのクランプ設置等で対応をします。また、検品などの手作業による工程のデータ取得では、様々な入力機器とつないでデータ取得を行います。